Thermal performance of different types of fins using convective heat transfer
A. R. Shinde, P. V. Patil, S. S Vhatkar, A. A. Kamble
Journal of Thermal and Fluid Science
Volume 2: Issue 1, March 2021, pp 31-37
Author's Information
A. R. Shinde1
Corresponding Author
1Student, Department of Mechanical Engineering, JSPM Narhe Technical Campus, Pune, Maharashtra, India
amitshinde049@gmail.com
P. V. Patil1, S. S Vhatkar1
2Student, Department of Mechanical Engineering, JSPM Narhe Technical Campus, Pune, Maharashtra, India
A. A. Kamble2
2Assistant Professor, Department of Mechanical Engineering, JSPM Narhe Technical Campus, Pune, Maharashtra, India
Abstract:-
This research examines the efficiency of various fin forms and includes heat transfer rate analysis. For analysis, four distinct fins are employed. Fins come in a variety of shapes, including round, square, hexagonal, and rectangular. The goal is to figure out how much heat is exchanged and how efficient a similar region with a different shape is. The goal of the research is to determine the maximum heat transfer from the fin surface as well as the efficiency of different fin shapes. The steady-state thermal analysis using ANSYS 14.5 is utilised for this investigation. Heat is transferred from a solid rod to a solid fin. Convection occurs with air flowing through a duct at the same time. The fin is used to mount a nichrome (band type) heater for heat delivery. The fins on the heater are composed of aluminum, which has a higher thermal conductivity than other materials. The solid work programme generates fin models, which are then loaded into ANSYS 14.5 . The investigation is carried out in a systematic manner. Lay out the experimental setup first, then obtain individual readings from various shaped fins. The heat transfer rate and efficiency are estimated from the recorded readings for various Reynolds' Numbers, and the results are then compared to other fins.Index Terms:-
Heat transfer, Fins, Thermal conductivity, thermal analysis, ANSYS 14.REFERENCES
- Seiyed E. Ghasemia, M. Hatamib, D. D. Ganji, “Thermal analysis of convective fin with temperature-dependent thermal conductivity and heat generation”, Case Studies in Thermal Engineering, Volume 4, November 2014, Pages 1-8. https://doi.org/10.1016/j.csite.2014.05.002
- Ugur Akyol, Kadir Bilen, “Heat transfer and thermal performance analysis of a surface with hollow rectangular fins”, Applied Thermal Engineering, Volume 26, 2006, pp. 209–216. DOI: 10.1016/j.applthermaleng.2005.05.014
- Hazim A. Al-Jewaree, “Experimentally Study the Effects of Fins Height and Space Ratio (H\S) to the Fin thermal performance by Natural Convections”, IOP Conference Series: Materials Science and Engineering, Volume 454, 2018. https://doi.org/10.1088/1757-899X/454/1/012128
- L.Prabhu, M.Ganesh Kumar, Prasanth M, Parthasarathy M, “Design and Analysis Of Different Types Of Fin Configurations Using ANSYS”, International Journal of Pure and Applied Mathematics, Volume 118 No. 5 2018, 1011-1017.
- Mladen Bošnjakovi´c and Simon Muhiˇ, “Numerical Analysis of Tube Heat Exchanger with Perforated Star-Shaped Fins”, Fluids, Volume 5, 2020. doi:10.3390/fluids5040242
To view full paper, Download here
To View Full Paper
For authors
Author's guidelines Publication Ethics Publication Policies Artical Processing Charges Call for paper Frequently Asked Questions(FAQS) View All Volumes and IssuesPublishing with
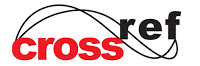
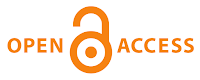
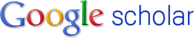
