Cutting Forces during Hard Turning for CBN Inserts: A Review
Bharatesh Akkiwad, N. V. Nanjundaradhya,Ramesh. S. Sharma, M. Rajanish
Volume 2: Issue 3, Sept 2015, pp 119-121
Author's Information
M. Rajanish2
Corresponding Author
2Department of Mechanical Engineering, Dayananda Sagar Academy of Tech & Mgmt-560082
prof.m.rajanish@gmail.com
Bharatesh Akkiwad, N. V. Nanjundaradhya, Ramesh. S. Sharma1
1Department of Mechanical Engineering, R.V.College of Engineering Bangalore-560059
Abstract:-
Tool life and machining surface roughness during hard turning are major components for industries because of the technical competitive world. Many researchers have worked to increase the life of the cutting tools and reduce the surface roughness of the workpiece only by experimental methods. But, the experimental techniques are of time consuming and destructive process. Hence there is a more scope for numerical investigations on hard turning. The objective of this work is to review the works carried out by different researchers both in experimental and numerical methods. Both experimental and numerical analysis work carried out for different combinations of varying cutting speed, feed rate and depth of cut for measuring the cutting forces.Index Terms:-
Tool life, machining, surface roughness, CADREFERENCES
- Manjot Singh Cheema “Investigation of effects of process parameters and insert geometry on hard turning of steels” Thesis submitted to Thapar University, Patiala.
- Khaider Bouacha et al. “Analysis and optimization of hard turning operation using cubic boron nitride tool” Int. Journal of Refractory Metals and Hard Materials 45 (2014) 160-178.
- Gaurav Bartarya et al. “Effect of cutting parameters on cutting force and surface roughness during finish hard turning AISI52100 grade steel” Procedia CIRP 1 (2012) 651 – 656.
- Hamdi Aouici et al. “Analysis of surface roughness and cutting force components in hard turning with CBN tool: Prediction model and cutting conditions optimization” Measurement 45 (2012) 344-353.
- H.M. Lin et al. “Wear behavior in turning high hardness alloy steel by CBN tool” Wear 264 (2008) 679–684.
- Vitor Augusto A. et al. “Turning of interrupted and continuous hardened steel surfaces using ceramic and CBN cutting tools” Journal of Materials Processing Technology 211 (2011) 1014–1025.
- J.P. Costes et al. “Tool-life and wear mechanisms of CBN tools in machining of Inconel 718” International Journal of Machine Tools & Manufacture 47 (2007) 1081–1087.
- W. Grzesik et al. “Machining of nodular cast iron (PF-NCI) using CBN tools” Procedia CIRP 1 (2012) 483 – 487.
- M.Kumara Swamy et al. “Modeling and Simulation of Turning Operation” ISSN: 2278-1684 Volume 3, Issue 6 (Nov-Dec. 2012), PP 19-26.
- Riaz Muhammad et al. “Finite Element Modelling of Conventional and Hybrid Oblique Turning Processes of Titanium Alloy” Procedia CIRP 8 (2013) 510 – 515.
- Christian Walter et al. “Structuring of CBN grinding tools by ultrashort pulse laser ablation” Procedia CIRP 14 (2014) 31–36.
- Hongtao Ding et al. “Multi-physics modeling and simulations of surface microstructure alteration in hard turning” Journal of Materials Processing Technology 213 (2013) 877– 886.
- V. Kryzhanivskyy et al. “Modelling and Experimental Investigation of Cutting Temperature when Rough Turning Hardened Tool Steel with PCBN Tools” Procedia CIRP 31 (2015) 489 – 495.
- Rajiv Kumar Yadav et al. “A simulation approach for estimating flank wear and material removal rate in turning of Inconel 718” Simulation Modelling Practice and Theory 52 (2015) 1–14.
- Girinon Mathieu et al. “3D stationary simulation of a turning operation with an Eulerian approach” Applied Thermal Engineering 76 (2015) 134-146.
- D.I.Lalwani et al. “Experimental investigations of cutting parameters influence on cutting forces and surface roughness in finish hard turning of MDN250 steel” journal of materials processing technology 206 (2008) 167–179.
- Mohamed Athmane Yallese et al. “Hard machining of hardened bearing steel using cubic boron nitride tool” Journal of materials processing technology 209 (2009) 1092–1104.
- Y. Sahin “Comparison of tool life between ceramic and cubic boron nitride (CBN) cutting tools when machining hardened steels” Journal of materials processing technology 209 (2009) 3478–3489.
- A.Srithar et al. “Experimental Investigation and Surface roughness Analysis on Hard turning of AISI D2 Steel using Coated Carbide Insert” Procedia Engineering 97 (2014) 72 – 77.
- Mehdi Remadna et al. “Evolution during time of tool wear and cutting forces in the case of hard turning with CBN inserts” Journal of Materials Processing Technology 178 (2006) 67–75.
- Anupam Agrawal et al. “Prediction of surface roughness during hard turning of AISI 4340 steel (69 HRC)” Applied Soft Computing 30 (2015) 279–286.
- E. Uhlmann et al. “Machining of high performance workpiece materials with CBN coated cutting tools” Thin Solid Films 518 (2009) 1451–1454.
- Y. Huang et al. “Cutting forces modeling considering the effect of tool thermal property-application to CBN hard turning” International Journal of Machine Tools & Manufacture 43 (2003) 307–315.
- Khaider Bouacha et al. “Statistical analysis of surface roughness and cutting forces using response surface methodology in hard turning of AISI 52100 bearing steel with CBN tool” Int. Journal of Refractory Metals & Hard Materials 28 (2010) 349–361.
- Dr. C. J. Rao et al. “Influence of cutting parameters on cutting force and surface finish in turning operation” Procedia Engineering 64 ( 2013 ) 1405 – 1415.
To view full paper, Download here .
To View Full Paper
For authors
Author's guidelines Publication Ethics Publication Policies Artical Processing Charges Call for paper Frequently Asked Questions(FAQS)Publishing with
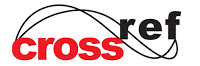
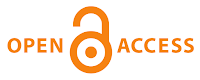
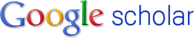
