Parametric Optimization of WEDM for Inconel-718 by using Taguchi - A Review
Niteen V. Patil, Manoj R. Patil, C. Chavan, Rajendra Shimpi
Volume 4: Issue 2, June 2017, pp 27-32
Author's Information
Niteen V. Patil1
Corresponding Author
1Department of Mechanical Engineering, R. C. Patel Institute of Technology, Shirpur, Maharashtra, India.
niteenpatil875@gmail.com
Manoj R. Patil2
2Department of Mechanical Engineering, R. C. Patel Institute of Technology, Shirpur, Maharashtra, India.
C. Chavan2, Rajendra Shimpi3
2,3Department of Mechanical Engineering, Mukesh Patel Technology Park, Shirpur, Maharashtra, India.
Abstract:-
Non tradition machining like EDM- Electro Discharge machine has no physical cutting forces present between the work piece and machining tool, high accuracy in metal removal process using thermal energy by generating a spark to erode the work piece. The work piece must be a conductive electricity material which is submerged into the dielectric fluid for better erosion. EDM has numerous application in die cavity casting with large components, small diameter whole having depth and various complex holes and other precision part. Inconel-718, a high strength, thermal resistant Nickel-based alloy, is mainly used in the aircraft industries. Inconel-718 has extreme toughness and work hardening characteristics of the alloy. The various notable works in the field of WEDM is reviewed in this paper and prominence given to Inconel-718.Index Terms:-
Electrical Discharge Machining (EDM), Inconel 718, WEDM, MRR, Taguchi method.REFERENCES
[1] Dubey A.K., Yadav V. "Multi objective optimization of Nd:YAG laser cutting of nickel-based superalloy sheet using orthogonal array with principal component analysis." Journal of Optics and Lasers in engineering, 2008, pp. 124-132.[2] Driver C., Atkinson J., Helml H.J., Lib L. "Micro EDM drilling of tapered holes for industrial applications." Journals of Material Processing Technology, 2004: pp. 296-303.
[3] Kanlayasiri K., Boonmung S. "Effects of wire EDM machining variables on surface roughness of newly developed DC 53 die steel: Design of experiments and regression model." Journals of Materials Processing Technology, 2007, pp. 459-464.
[4] Lin Y.C., Chen Y.F., Wang D.A., Lee H.S. "Optimization of machining parameters in magnetic force assisted EDM based on Taguchi method",Journals of Materials Processing, 2009, pp.3374-3383.
[5] Luis C.J., Puertas I. "Methodology for developing technological tables used in EDM processes of conductive ceramics”, Journals of Material Processing Technology, 2007, pp. 189-197.
[6] Mahendran S., Devarajan R., Nagarajan T., Majdi A. "A Review of Micro EDM." Journals of materials processing, 2010: pp. 87-94.
[7] Puertas I., Luis C.J., Alvarez L., "Analysis of influence of EDM parameters on surface quality, MRR and EW of WC-Co",Journals of Material Processing Technology, 2004: pp. 1026-1032.
[8] Rajmohan T., Prabhu R., Subba Rao. "Optimization of machining parameters in electrical discharge machining of 304 stainless steel”,Juornal of Procedia engineering, 2012: pp. 1030-1036.
[9] Seong Min Son, Hanseok Limb, Kumar A.S., Rahman M. "Influences of pulsed power condition on the machining properties in micro EDM." Journals of Material Processing Technology, 2007: pp. 73-76.
[10] Shankar Singh, Maheshwari S., Pandey P.C. "Some investigations into the electric discharge machining of hardened tool steel using different electrode materials", Journals of Material Processing Technology, 2004: pp. 272-277.
[11] Somnath M. Kale and D. S. Khedekar “Optimization of Process Parameters in Electric Discharge Machining Of Inconel 718 by Using Copper Electrode” IOSR Journal of Mechanical and Civil Engineering Vol. 13, Issue 3 Ver. III,May- Jun. 2016, PP 51-55.
[12] Sushil Kumar Choudhary and Dr. R.S Jadounb,“Current Advanced Research Development of Electric Discharge Machining: A Review”, International Journal of Research in Advent Technology, Vol.2, No.3, March 2014, pp.2321-9637.
[13] Tai T.Y., Masusawa T., Lee H.T. "Drilling micro holes in hot tool steel by using Micro Electric Discharge Machining." Journals of Materials Processing, 2007: pp205-210.
[14] Yan B.H., Wang A.C., Huang C.Y., Huang F.Y.,. "Study of precision micro holes on borosilicate glass using micro EDM combined with micro ultrasonic vibration machining." InternationalJournal of Machine Tools & Manufacture, 2002: pp.1105-1112.
To view full paper, Download here
To View Full Paper
For authors
Author's guidelines Publication Ethics Publication Policies Artical Processing Charges Call for paper Frequently Asked Questions(FAQS) View all Volumes and IssuesPublishing with
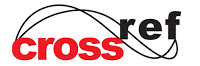
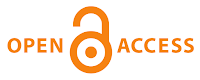
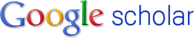
